Sample Preparation for Cast Iron - Crankshaft
Sample Preparation for Cast Iron - Crankshaft
Cast iron refers to those iron-carbon-silicon alloys which contain 2.5% - 4% carbon and usually 1-3% silicon. Cast iron is an important engineering material with a number of advantages, mainly good castability and machinability and moderate mechanical properties. Because of its economical advantages cast iron is used for many applications in the automotive and engineering industry. In addition, specific cast irons are the material of choice for sea water pump housings, rolling mill rolls and parts for earth moving equipment.
As the morphology of graphite has a major influence on the mechanical properties of cast iron, metallographic quality control of grey iron is an integral part of its production process. Using standard reference comparison charts and/or image analysis techniques, the morphology, size and distribution of the graphite is determined on an unetched, polished sample. Depending on the specification, the sample is then etched to check the structure of the matrix.
Recommendations for the preparation of cast iron
Cutting: For sectioning hard, white cast irons a CBN (cubic boron nitride) wheel is recommended. For large sections automatic cutting is more efficient than manual cutting. For cutting cast irons with graphite it is recommended to select an aluminium oxide wheel (FS-Max, FS-Medium, FS-Soft types) according to the hardness of the cast iron to be cut.
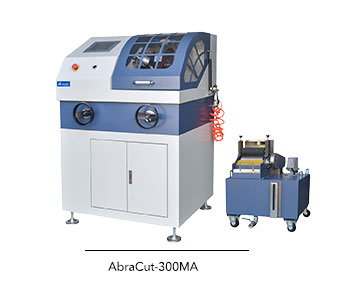
Mounting: Quality control samples are usually prepared unmounted. For failure analyses samples it is recommended to use hot compression mounting. For soft to medium hard cast irons a phenolic resin (MetBak-100) is recommended, for harder types of cast irons a reinforced resin(MetEpo-200) is more suitable.
Grinding and polishing:
In general, cast irons with graphite have been ground with silicon carbide abrasive paper. Now diamond grinding disc has replaced silicon carbide abrasive paper for fine grinding most cast irons as it keeps the samples very flat and doesn’t leave the graphite in relief. Hard white cast irons and ADI iron can be plane ground with diamond disc (Dia-M) and also fine ground with diamond disc (Dia-R). Soft and medium hard cast irons with a ferritic, austenitic or pearlitic matrix are plane ground with silicon carbide abrasive paper and fine ground with diamond disc (Dia-R).
For cast irons that tend to corrode during polishing it is recommended to use water free diamond suspension, A, and yellow lubricant.
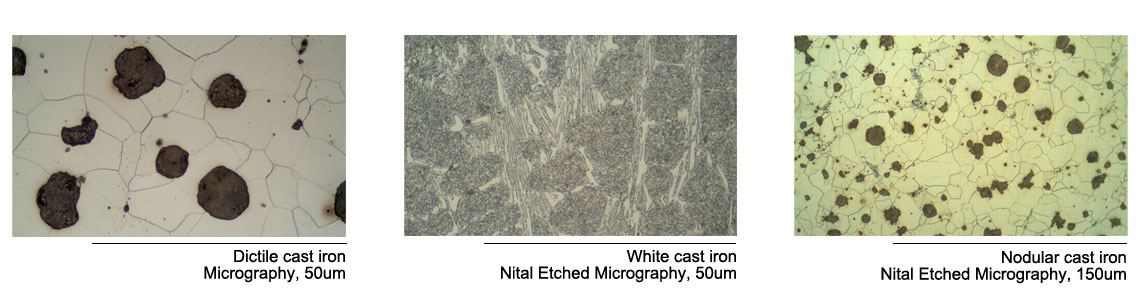
Cast iron refers to those iron-carbon-silicon alloys which contain 2.5% - 4% carbon and usually 1-3% silicon. Cast iron is an important engineering material with a number of advantages, mainly good castability and machinability and moderate mechanical properties. Because of its economical advantages cast iron is used for many applications in the automotive and engineering industry. In addition, specific cast irons are the material of choice for sea water pump housings, rolling mill rolls and parts for earth moving equipment.
As the morphology of graphite has a major influence on the mechanical properties of cast iron, metallographic quality control of grey iron is an integral part of its production process. Using standard reference comparison charts and/or image analysis techniques, the morphology, size and distribution of the graphite is determined on an unetched, polished sample. Depending on the specification, the sample is then etched to check the structure of the matrix.
Recommendations for the preparation of cast iron
Cutting: For sectioning hard, white cast irons a CBN (cubic boron nitride) wheel is recommended. For large sections automatic cutting is more efficient than manual cutting. For cutting cast irons with graphite it is recommended to select an aluminium oxide wheel (FS-Max, FS-Medium, FS-Soft types) according to the hardness of the cast iron to be cut.
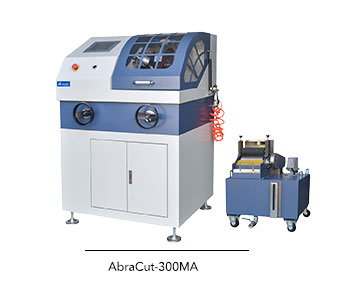
Mounting: Quality control samples are usually prepared unmounted. For failure analyses samples it is recommended to use hot compression mounting. For soft to medium hard cast irons a phenolic resin (MetBak-100) is recommended, for harder types of cast irons a reinforced resin(MetEpo-200) is more suitable.
Grinding and polishing:
In general, cast irons with graphite have been ground with silicon carbide abrasive paper. Now diamond grinding disc has replaced silicon carbide abrasive paper for fine grinding most cast irons as it keeps the samples very flat and doesn’t leave the graphite in relief. Hard white cast irons and ADI iron can be plane ground with diamond disc (Dia-M) and also fine ground with diamond disc (Dia-R). Soft and medium hard cast irons with a ferritic, austenitic or pearlitic matrix are plane ground with silicon carbide abrasive paper and fine ground with diamond disc (Dia-R).
For cast irons that tend to corrode during polishing it is recommended to use water free diamond suspension, A, and yellow lubricant.
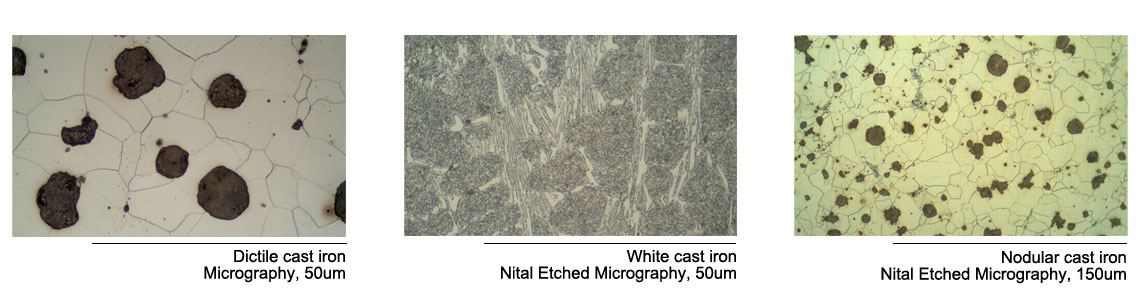
- Previous:Sorry, no more.
- Next:Sorry, no more.
Send your message to us:
